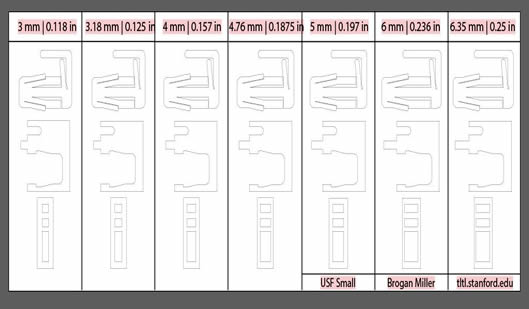 |
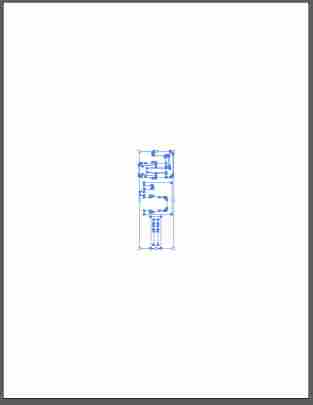 |
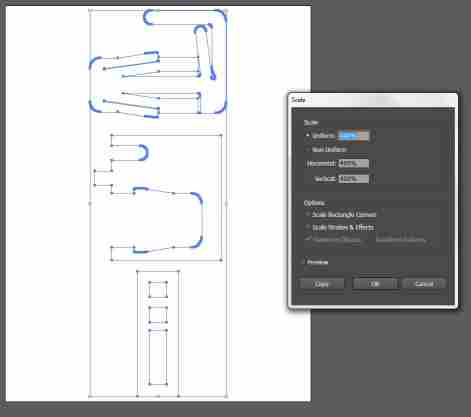 |
Figure 1: Tutorial File Downloaded and Uploaded to Adobe Illustrator |
Figure 2: New File Created in AI with Chosen Thickness of Material |
Figure 3: Resized Design |
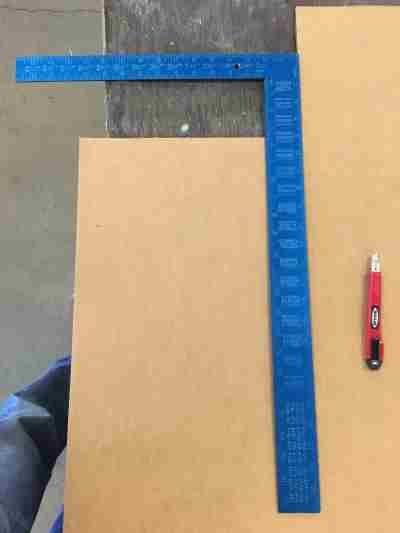 |
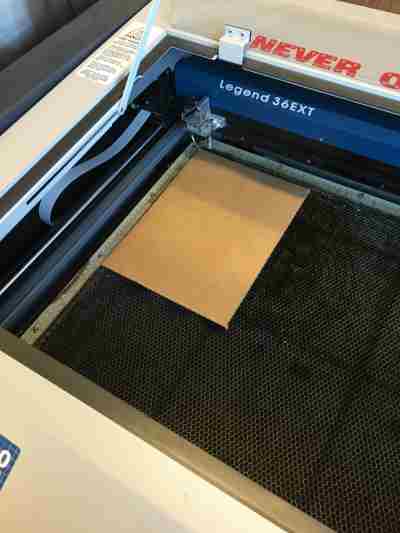 |
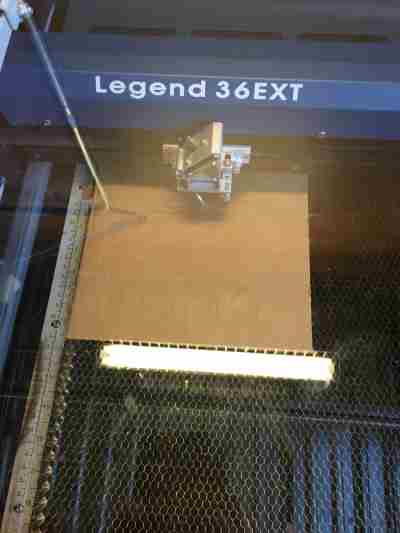 |
Figure 4: Measuring Out Piece of Cardboard for Laser Cutter |
Figure 5: Measured out Piece Placed into Laser Cutting Machine |
Figure 6: Laser Cutter Working its Magic |
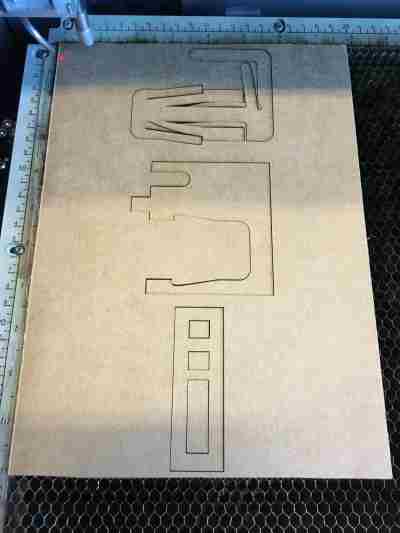 |
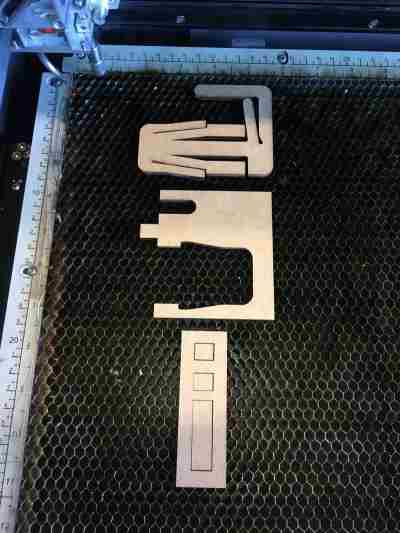 |
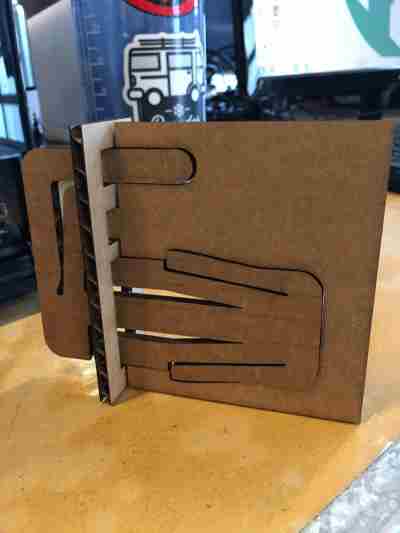 |
Figure 7: Laser Cutter Done Printing on Cardboard |
Figure 8: Pieces Popped Out of Cardboard |
Figure 9: Finished Pieces Put Together |